


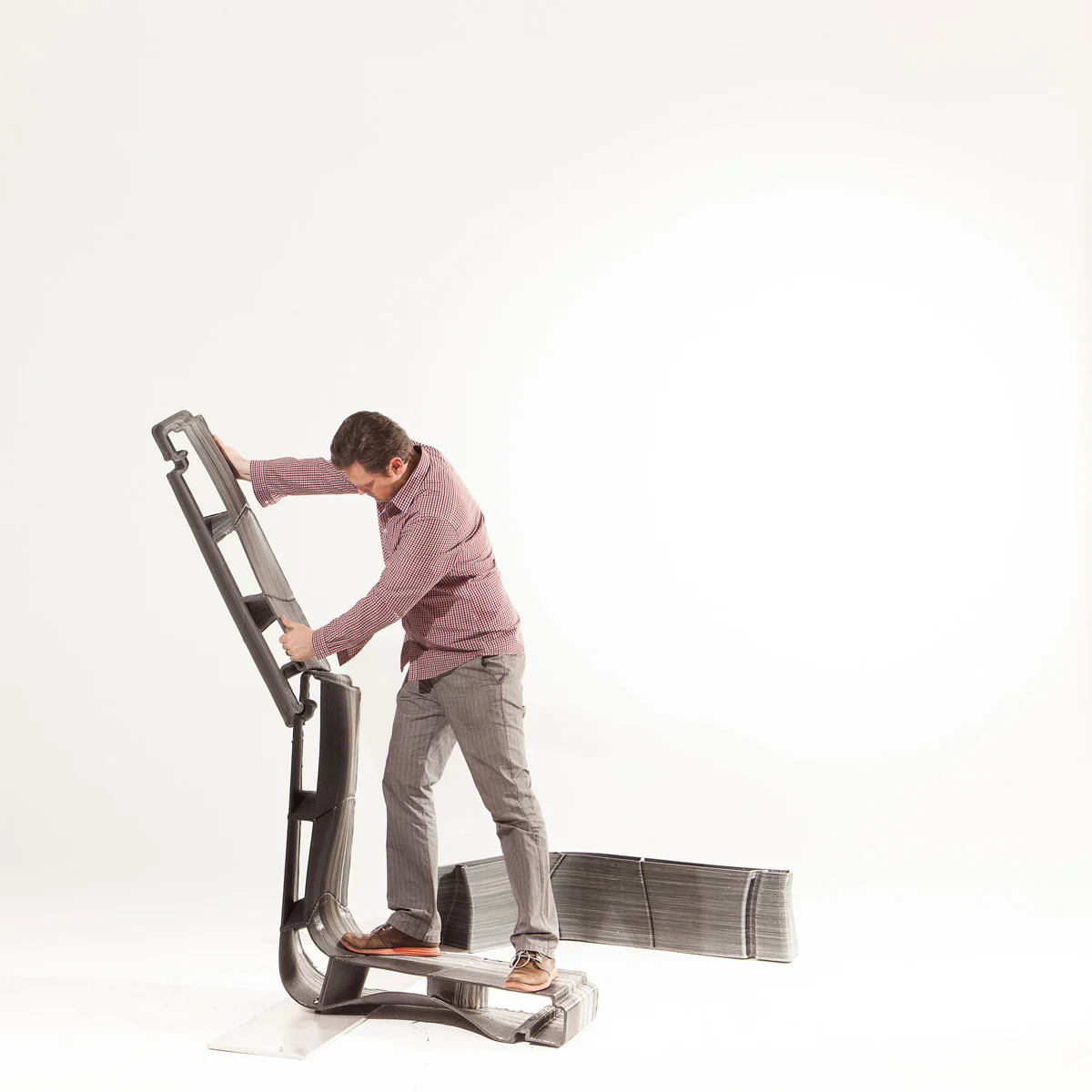
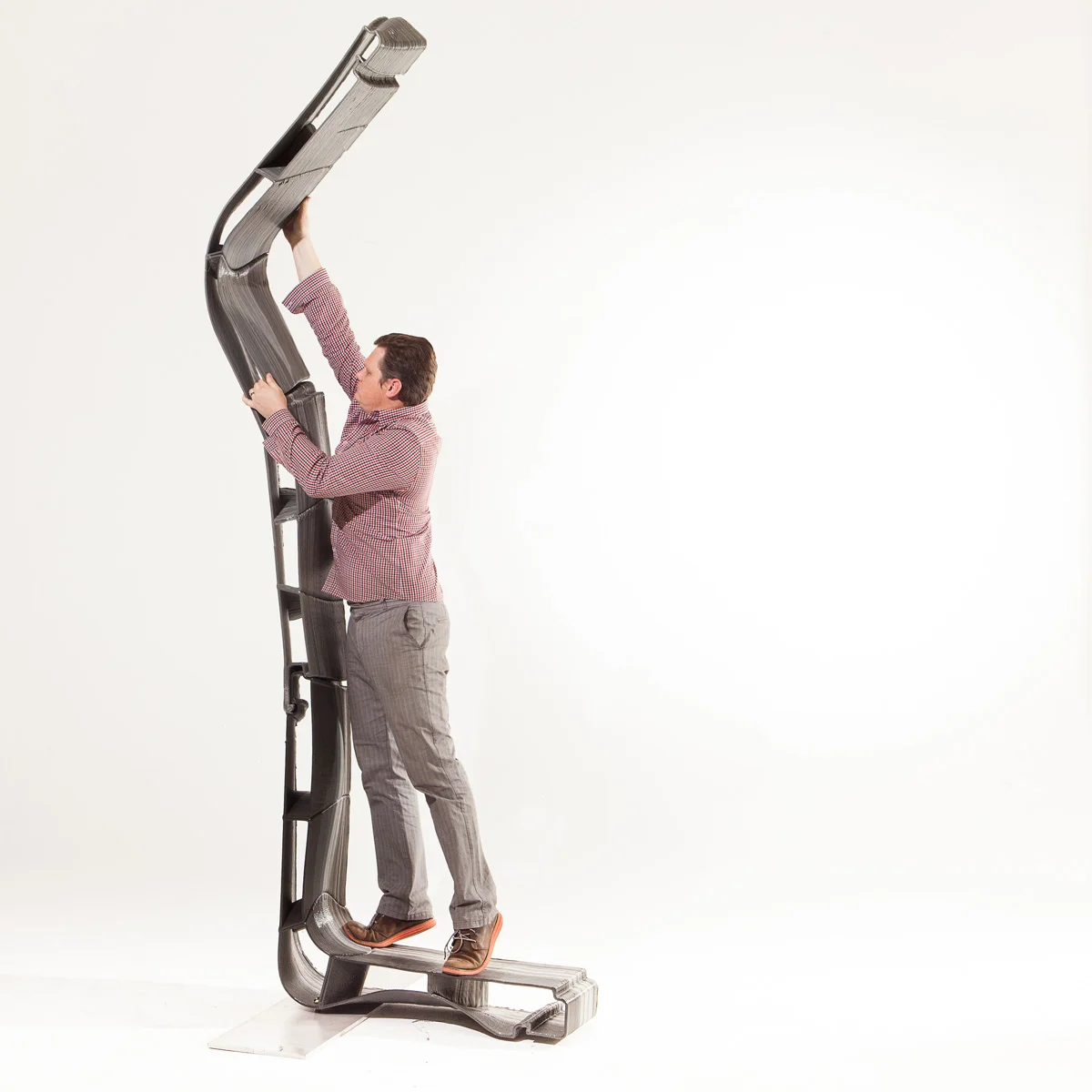

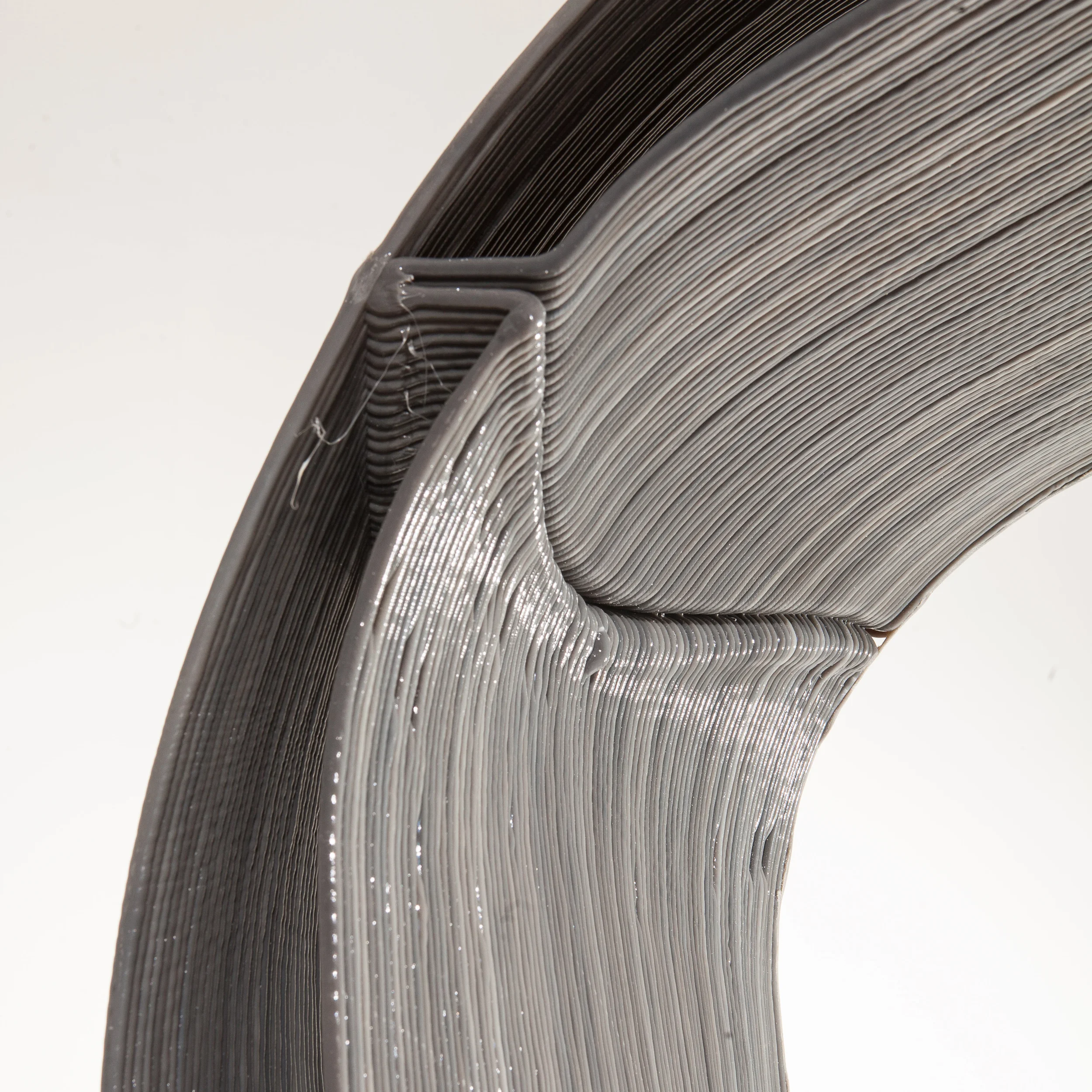
Your Custom Text Here
This prototype building system was developed by Zachary Schoch with support from Eugene Lee and was Exhibited at 3D PrinterWorld 2015 in Burbank California. It fit into one car and took about 10 minutes to setup including unloading. Standing over 10 feet tall it was printed at full scale utilizing the Euclid robot 3d printer.
These three 3D printed pieces took a total of less than 18 hours to print, and use high strength ABS plastic.
all photography by Nicole Caldwell
This prototype building system was developed by Zachary Schoch with support from Eugene Lee and was Exhibited at 3D PrinterWorld 2015 in Burbank California. It fit into one car and took about 10 minutes to setup including unloading. Standing over 10 feet tall it was printed at full scale utilizing the Euclid robot 3d printer.
These three 3D printed pieces took a total of less than 18 hours to print, and use high strength ABS plastic.
all photography by Nicole Caldwell
Quick assembly of units by hand takes less than a minute.
Example of a small but full scale structure that is readily printable with the S-Wall system. Rendering by Eugene Lee
Modular 3D printed full scale building system featuring large high strength ABS components that structurally snap together allowing for easy transport and assembly by hand. Total print time for these three pieces was less than 18 hours. Assistance with printing and 3d modeling for s-wall from Eugene Lee.
Because these components are built from such high performance material they should be constructible by hand, or for larger and more structurally elements only minimal equipment would be required. This property allows for investment in higher performance printing facilities due to the low cost of transportation to the building site.
With this construction system there is no fundamental difference between the traditionally disparate elements of floor/wall/roof. In this instance the floor literally becomes the wall, and the wall becomes the roof/ceiling.
Because the s-wall system is hollow, mechanical systems can be integrated directly into it. Piping for liquids could be installed readily after assembly using flexible tubing, or pipes could be printed integral to the s-wall. Ventilation ducts would also be printed integral to the unit with vents being able to be printed simultaneously as well, in the floors, wall or roof depending on the need.
Detail view of s-wall connection. This detail was designed to have a tension element on the outside of the building (hook and matching receptacle left center) and a compression element on the inside. The joint is simply disconnected by reversing the load path.
This detail shows the webbing that is integrally printed to structurally connect the inside and outside skins, acting in a similar manner as the diagonals in a truss.
Because the tension element (outer seam) is placed below the compression element (inner seam) the snap connection should prevent any water intrusion. Additionally a sealing gasket could be integrated into the connection to prevent vapor and air intrusion.
By curving the web connection in elevation and rotating it along its length the web is acting in multiple planes simultaneously - greatly increasing it rigidity while minimizing the use of material and reducing the print time.